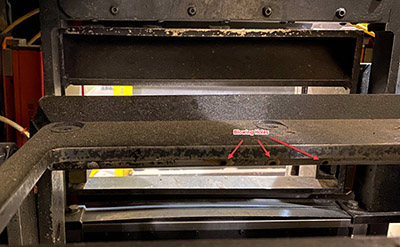
It is very common in an industrial facility to have compressed air blowing applications installed at various locations to provide cleaning of sensing eyes and scanners. But it is important to keep in mind that this blowing demand can add up quickly — especially if there are many of these applications installed within the plant.
One thing about compressed air is that it is quite expensive for the mechanical force you get using a blow nozzle. Another thing is that the cleaning action does not necessarily need to be continuous.
Consider the compressed air blowing device shown in Fig. 1. This homemade pipe with holes drilled in it consumed 30 cfm continuously, costing about $5,800 per year to operate. There were a total of four of these devices in the plant.
Experiments were done with this device, and it was determined a 0.5 second blast of compressed air every minute was sufficient to keep the scanner platen clean. A timer-controlled solenoid was installed to accomplish this action. Now, the average flow of this device has dropped by a factor of 120 — to only one-quarter of a cfm, saving $5,700 per year!
Plant personnel were impressed by the savings and are considering installing additional timer controls and special valves that can provide rapid pulsing on devices that need more or less continuous blowing. Changing a continuous blow to one that pulse a few times per second, with 50% dwell between pulse can provide enhanced cleaning, due to the turbulence that is introduced, yet consume less compressed air, reducing the cost of operation.
Some possible sources for such valves are here:
SMC pulse blowing valve
Parker Hannifin air saving valve
Interested in seeing how this all works? Go to this video to watch.
Continuous blowing is not always the best solution if compressed air must be used for cleaning. The secret to optimization is controlling the duty cycle.
Filed Under: Compressed Air Technologies, Pneumatic Tips