By Ron Marshall
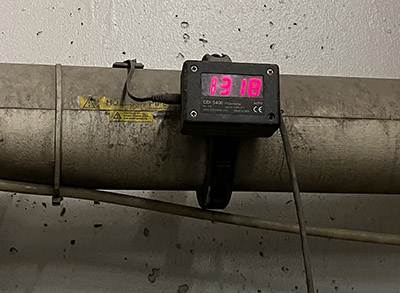
Compressed air is one of the most expensive ways to supply energy to facility tools and equipment. This is due to the inherent inefficiencies in the process of compressing air — the biggest product is heat and the secondary output is compressed air. While this is disappointing, there are still things that can be done to keep your compressed air system costs as low as possible. Here are six key suggestions to improve your facility:
- Baseline (measure) your system — Most people have no idea how much energy their air compressors are consuming and how much compressed air they are using. The trick to managing a compressed air system is to measure it. This measurement can tell you the costs and point out some problems such as poor compressor control or high levels of leakage.
- Fix your leaks — Leakage waste is one of the biggest costs in a compressed air system and something that can most easily be addressed by anyone that is handy with tools. But don’t try to hunt for leaks with your naked ears. There are readily available and affordable ultrasonic leak detection instruments that you can use to give yourself super-hearing. This way, you can locate even the smallest of leaks in noisy environments. But realize, you must control your compressors optimally to gain the most out of leak repair.
- Eliminate wasteful end uses — Because compressed air is so expensive, about 7 to 8 horsepower goes into producing one horsepower of mechanical energy at the end use. Thus, it is a good idea to look for and eliminate wasteful items that can best be supplied by some other energy source such as direct drive electrical or hydraulic power. If the compressed air demand can’t be eliminated, then see what you can due to reduce the duty cycle. Control the demand by automatically turning it off with electrical switches (or manually) when it is not required — say, during evenings or weekends.
-
Fig. 2. Ultrasonic leak detector guns are a very effective in finding system waste. Both leaks and inappropriate uses of compressed air can be found using these affordable tools. Lower your pressure — Reducing the pressure at the discharge of an air compressor will reduce its power consumption per unit output by about 1% for every 2-psi reduction. A secondary benefit is that the flow of compressed air to any unregulated compressed air use reduces by about 1% for every 1 psi of lower pressure. Use this fact to save yourself some energy costs.
- Better control your compressors — There are many ways to control compressed air systems, some more efficient than others. Old school compressor control methods operate using a very inefficient modulating mode that can make partially loaded compressors consume two or three times the energy needed. More efficient control modes use load/unload, variable displacement, start/stop, and variable frequency drive. If you don’t know how your compressors are being controlled, ask your service provider; there may be something that can be done to save costs.
- Educate yourself on compressed air optimization, then take action — There are lots more things that can be improved in a compressed air system besides these six things and the best way to find out is to take some great training. Have a look at the online training that is available from Compressed Air & Gas Institute (www.cagi.org) and the Compressed Air Challenge (www.compressedairchallenge.org) and sign up. Learn the steps required to improve your system then take action!
You are invited to attend a free webinar put on by Compressed Air Challenge on February 16th that discusses these six points in more detail.
Filed Under: Components Oil Coolers, Compressed Air Technologies, Engineering Basics, Pneumatic Tips