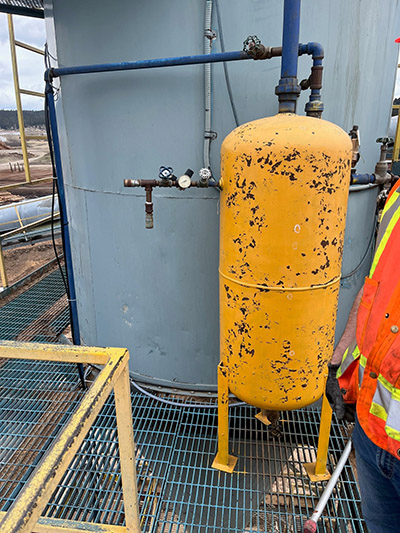
A wood products company decided to conduct a treasure hunt for energy savings on its compressed air system. Plant personnel were scheduled to have a production outage during a one-week period — and so they invited a compressed air expert to help them identify any suggested improvements to the system.
Industrial plants frequently have staff exercises that they call energy “treasure hunts,” where their own personnel, under the direction of an expert, explore their facility and brainstorm ideas for improvements that might save energy. This study was focused on the compressed air system, and the resulting efforts definitely dug up some valuable “treasure.”
In participating in an energy treasure hunt on a compressed air system, participants need to be very observant, using both their eyes and ears to detect problems. Once the staff started to explore the site, it wasn’t long before they started to notice some curious sounds and sights:
- The site had a heatless desiccant dryer installed. These types of dryers frequently have a purge flow setting that is controlled by a ball valve to a certain pressure on a purge pressure gauge. The specified purge pressure was supposed to be 45 psi. However, staff noticed it was incorrectly adjusted to 60 psi (the correct adjustment is on a tag on the gauge). This higher pressure resulted in about 17 cfm in extra purge flow, costing about $3,000 in extra energy consumption per year.
- Some air-operated diaphragm pumps were found excessively cycling to pump condensate for steam; the staff noticed these pumps sounded quite strange. The group found these were actually pumping nothing most of the time, but excessively cycling while continuously consuming about 30 cfm of compressed air, costing about $5,300 per year.
- The study group found “gold” when someone taking a break outside noticed a regular whooshing sound at 30 second intervals far up on a dust collector and decided to investigate. They found a storage receiver, appropriately painted yellow (like gold), with a faulty pressure relief valve. The operation of this valve was found to be wasting 90 cfm of compressed air flow costing $16,000.
This $24,000 worth of energy savings was not bad for a day’s work! And more than enough to afford plentiful refreshments to celebrate the treasure hunt success.
Filed Under: Components Oil Coolers, Compressed Air Technologies, Pneumatic Tips